X-ray Sources 101: Taking Faster Images at Higher Resolution (Part 2)
Before jumping into today’s post discussing Micro X-Ray’s unique diamond anode and how it can speed up your imaging applications, here’s a little background reading:
In Part 1, we followed the path of an X-ray from generation inside the tube through detection on a single pixel of an X-ray detector. We discussed the probabilities around the X-ray making it to the detector, and we learned that if you increase the amount of X-rays generated, then you decrease the time required to take an X-ray image.
So, what if you want to halve the image acquisition time? It should be as easy as turning up the power, right? As with all X-ray questions, the answer is yes, but…
Power Loading
In this case, the “but” is power loading causing damage to the target. The smaller the spot size, the tighter the concentration of power within the target disk. If you’ve ever played with a magnifying glass in the summer, you’ll already be familiar with this concept.
A magnifying glass focuses the sun’s rays which are otherwise evenly spread over the diameter of the glass and, when held at the right distance from the ground, focuses those rays down to a very small and bright focal spot. Those same rays that were spread out evenly over the diameter of the magnifying glass which may have caused a minor sunburn after a half hour or so, when concentrated into a small focal spot now have the potential to start fires and melt crayons within seconds. You can adjust the focal spot of the magnifying glass to create a very small and bright spot, or a less small and less bright spot by changing the geometric optics (moving the magnifying glass up and down in space).
Similarly, the power in the electron beam, is concentrated using electrostatic optics into a focal spot on the X-ray tube’s anode. The power of the electron beam is given in W, and the focal spot size is given in microns. We can divide the two to get a power loading factor expressed in Watts per micron (W/μm). This can be thought of as the “brightness” of the spot. If you increase the beam power but keep the spot size constant, the brightness increases. Similarly, if you decrease the spot size but keep the power constant, you will also increase the brightness. So why not just make an infinitely small spot with as much power as your detector can handle?
Target Material Selection
Depending on the properties of the target material, the target face can handle more or less power before failure. When a target fails, or becomes pitted, the intensity of the spot damages the target material and burns a hole through the target disk down to the anode substrate, which has the effect of reducing the flux intensity in the spot to a fraction of its value. The image above shows a undamaged target and a pitted target on the same scale – notice that the spot intensity in the center of the undamaged target’s spot actually exceeds the detector’s 16k counts, while the pitted target has a maximum intensity of under 6k counts. This is because the center, brightest point in the spot has burned through the target disk and is no longer producing X-rays.
Thinking back to our magnifying glass example, the same focal spot size under the magnifying glass can burn skin, cause paper to combust, and cause absolutely no damage to concrete. The difference isn’t the power in the focal spot, it’s the durability of the material the focal spot is concentrated on.
Different X-ray target materials all have different properties. Tungsten (W) is a common X-ray target because it not only produces a nice clean Bremsstrahlung radiation profile, but it also happens to be a quite durable metal with a high melting point. Conversely, Gold (Au) produces very useful peaks in certain XRF applications, but it is such a soft metal that a relatively dim focal spot (ie, low power loading) will cause damage to the target material, resulting in such low achievable count rates as to negate its benefits in all but the most specialized of applications.
Because W is the common choice of target material for imaging applications, we’ll focus on W target sources. A safe rule of thumb for power loading on a standard W target X-ray tube is 1W/μm. Beyond 1W/μm, the spot will generate too much power for the target to handle, and the target disk will be damaged, sometimes in a matter of seconds. Micro X-Ray has developed a unique target material structure using a Diamond substrate to move the heat out of the spot and into the anode much more efficiently than a standard target structure. This allows us to run at a 50% increase in power loading compared to a non-Diamond backed target, allowing for a 1.5W/μm power loading number.
Higher Power Loading Enabling Faster Images
What does this all mean? If we remember from Part 1, the more photons you have hitting your detector, the faster you can get an image. If you need, for example, 10 million photons to hit your detector, you can get there 50% faster by increasing the power by 50%. And with our diamond target, you can do just that, and accumulate your 10 million counts faster to increase your line speed.
Alternatively, what if you have a fixed amount of time in your process in order to take an image? Our Diamond target can help there, too, by allowing you to reduce the focal spot size while keeping the power consistent. This will result in a higher resolution image in your defined process time.
Micro X-Ray Diamond Anode Products
Both our Microbox integrated X-ray source and our Seeray water-cooled X-ray tube contain our unique Tungsten/diamond anode technology.
In the case of the Microbox, this allows us to run at an industry-leading power loading of 1.5W/μm, enabling faster and crisper images than our competitors. Whether you’re interested in maximizing the power at a given spot size, or maximizing the resolution in a given exposure time, the Microbox’s 1.5W/μm power loading will give you measurable improvements against any other Microfocus source on the market.
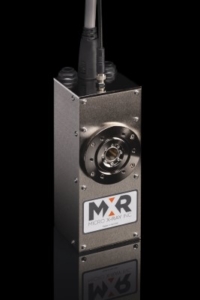
In the case of the Seeray, our diamond anode technology is coupled with a unique direct water-cooled anode. This allows for the same 1.5W/μm power loading as the Microbox source, while the direct anode cooling allows for beam powers of 100W or more. The direct anode cooling also enables super-fast beam stabilization times, making this an ideal tube for X-ray optic coupling and single crystal XRD.
For More Information on Diamond Anodes
We’re always available to talk about X-rays, and help you weigh the tradeoffs and consider the various application constraints to pick the right source for you. Reach out to us today to talk about how our diamond anode technology can be put to use to optimize your X-ray application today!